Asphalt plants play a crucial role in the construction industry, providing the necessary materials for quality pavements. From the raw materials to the final product, these plants are responsible for the production of asphalt, which is used in road construction and maintenance. This article will explore the process of asphalt production, highlighting the importance of quality control and the various stages involved in creating durable and long-lasting pavements.
The Importance of Asphalt Plants in the Construction Industry
Asphalt plants play a crucial role in the construction industry. They are responsible for producing asphalt, a key material used in road construction. Asphalt is a durable and flexible material that provides a smooth and safe driving surface. Without asphalt plants, it would be impossible to build and maintain roads, highways, and other infrastructure projects. These plants are equipped with state-of-the-art technology and machinery to ensure the production of high-quality asphalt. They also adhere to strict environmental regulations to minimize their impact on the environment. In conclusion, asphalt plants are essential for the construction industry as they provide the necessary material for building and maintaining our transportation networks.
Understanding the Raw Materials Used in Asphalt Production
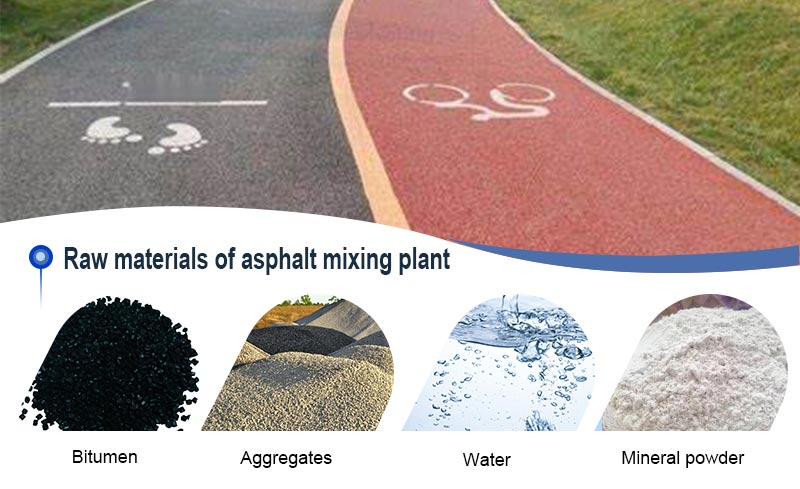
Asphalt production involves the use of various raw materials that are essential for creating a durable and high-quality product. One of the main components of asphalt is bitumen, a sticky black substance derived from crude oil. Bitumen acts as a binder, holding the other materials together and providing flexibility and strength to the asphalt. Aggregates, such as crushed stone, sand, and gravel, are also crucial in asphalt production. These materials provide stability and strength to the asphalt mixture. Additionally, additives like polymers and fibers may be used to enhance the performance and durability of the asphalt. Understanding the raw materials used in asphalt production is vital for ensuring the production of long-lasting and reliable asphalt pavements.
The Process of Asphalt Production: From Mixing to Heating
Asphalt production is a complex process that involves several stages, from mixing to heating. The first step is the mixing of aggregates, such as sand, gravel, and crushed stone, with asphalt cement. This mixture is then heated to a high temperature to ensure proper blending and to remove any moisture. The heated mixture is then transported to the construction site, where it is laid and compacted to form a smooth and durable surface. Throughout the process, quality control measures are implemented to ensure that the asphalt meets the required specifications. Overall, the process of asphalt production requires careful attention to detail and adherence to strict standards to produce a high-quality and long-lasting product.
Quality Control Measures in Asphalt Plants: Ensuring Durability and Performance
Quality control measures play a crucial role in ensuring the durability and performance of asphalt plants. These measures involve a series of tests and inspections that are conducted throughout the production process to ensure that the asphalt meets the required specifications and standards. One of the key quality control measures is the testing of raw materials, such as aggregates and bitumen, to ensure their quality and suitability for asphalt production. Additionally, regular testing of the asphalt mix is conducted to check its consistency, density, and other physical properties. This helps in identifying any potential issues or deviations from the desired quality, allowing for timely adjustments and improvements. Overall, implementing effective quality control measures is essential for producing high-quality asphalt that can withstand the demands of various applications and provide long-lasting performance.
Environmental Considerations in Asphalt Plant Operations
Asphalt plant operations have a significant impact on the environment, and it is crucial for operators to consider environmental considerations in their operations. One of the main environmental concerns is air pollution. Asphalt plants emit various pollutants, including volatile organic compounds (VOCs), particulate matter, and greenhouse gases. These pollutants can have detrimental effects on air quality and human health. To mitigate these impacts, operators can implement measures such as using advanced emission control technologies, regularly maintaining equipment to minimize emissions, and ensuring proper storage and handling of materials. Additionally, water pollution is another concern, as asphalt plants generate wastewater that can contain harmful chemicals. Operators should implement proper wastewater management practices to prevent contamination of nearby water bodies. Overall, considering environmental factors in asphalt plant operations is essential to minimize the industry’s impact on the environment and promote sustainable practices.
Innovations in Asphalt Plant Technology: Improving Efficiency and Sustainability
Asphalt plants play a crucial role in the construction industry, producing the material needed for roads, highways, and other infrastructure projects. In recent years, there have been significant innovations in asphalt plant technology, aimed at improving efficiency and sustainability. One such innovation is the use of warm mix asphalt (WMA), which allows for lower production temperatures and reduced energy consumption. This not only saves costs but also reduces greenhouse gas emissions. Additionally, advancements in plant automation and control systems have improved the accuracy and consistency of asphalt production, resulting in higher quality materials. These innovations are helping the industry meet its sustainability goals while also improving overall efficiency.
Conclusion
In conclusion, asphalt plants play a crucial role in the production of quality pavements. From the sourcing of raw materials to the careful blending and heating processes, these plants ensure that the asphalt produced meets the necessary standards. With advancements in technology and a focus on sustainability, asphalt plants continue to evolve and contribute to the development of durable and environmentally-friendly road surfaces.
What are asphalt plants?
Asphalt plants are facilities where asphalt is produced by mixing aggregates, binder, and filler materials. These plants are used to manufacture asphalt for various construction projects, such as roads, highways, and parking lots.
What are the raw materials used in asphalt production?
The raw materials used in asphalt production include aggregates (such as crushed stone, gravel, and sand), binder (typically asphalt cement or bitumen), and filler materials (such as limestone dust or hydrated lime). These materials are carefully selected and mixed in specific proportions to achieve the desired asphalt quality.
How does the asphalt production process work?
The asphalt production process starts with the heating of aggregates in a drum or batch plant. The heated aggregates are then mixed with binder and filler materials in the plant’s mixer. The resulting mixture, known as hot mix asphalt (HMA), is then transported to the construction site for paving.
What factors affect the quality of asphalt produced?
Several factors can affect the quality of asphalt produced, including the quality and gradation of aggregates, the type and amount of binder used, the mixing temperature, and the mixing time. Proper control and monitoring of these factors are essential to ensure the production of high-quality asphalt.
What are the different types of asphalt plants?
There are several types of asphalt plants, including drum mix plants, batch plants, and continuous mix plants. Drum mix plants have a continuous mixing process, while batch plants mix asphalt in batches. Continuous mix plants combine the drying and mixing processes in a single unit.
How is the quality of asphalt pavement ensured?
The quality of asphalt pavement is ensured through various quality control measures. These include regular testing of raw materials, monitoring of the asphalt production process, and conducting performance tests on the finished pavement. Additionally, adherence to industry standards and specifications is crucial to ensure the quality of asphalt pavements.