Capping and sealing equipment plays a crucial role in ensuring the security and tamper-proofing of various packaging materials. These machines are designed to efficiently and effectively seal containers such as bottles, jars, and tubes, preventing any unauthorized access or tampering. With advancements in technology, capping and sealing equipment now offer a wide range of options, allowing industries to achieve higher levels of product integrity and consumer trust.
1. Introduction to Capping and Sealing Equipment: Enhancing Packaging Security
Capping and sealing equipment play a crucial role in enhancing packaging security. As a packaging professional, I understand the importance of ensuring that products are securely sealed before they reach consumers. This not only helps in maintaining product quality but also prevents tampering and ensures customer satisfaction. Capping and sealing equipment are designed to provide airtight and leak-proof seals, keeping the contents of the package intact and protected. From bottles to jars and tubes, these machines offer a wide range of options for different packaging needs. In this article, we will explore the various types of capping and sealing equipment available in the market and how they can benefit businesses in the packaging industry.
2. Understanding the Importance of Secure and Tamper-Proof Packaging
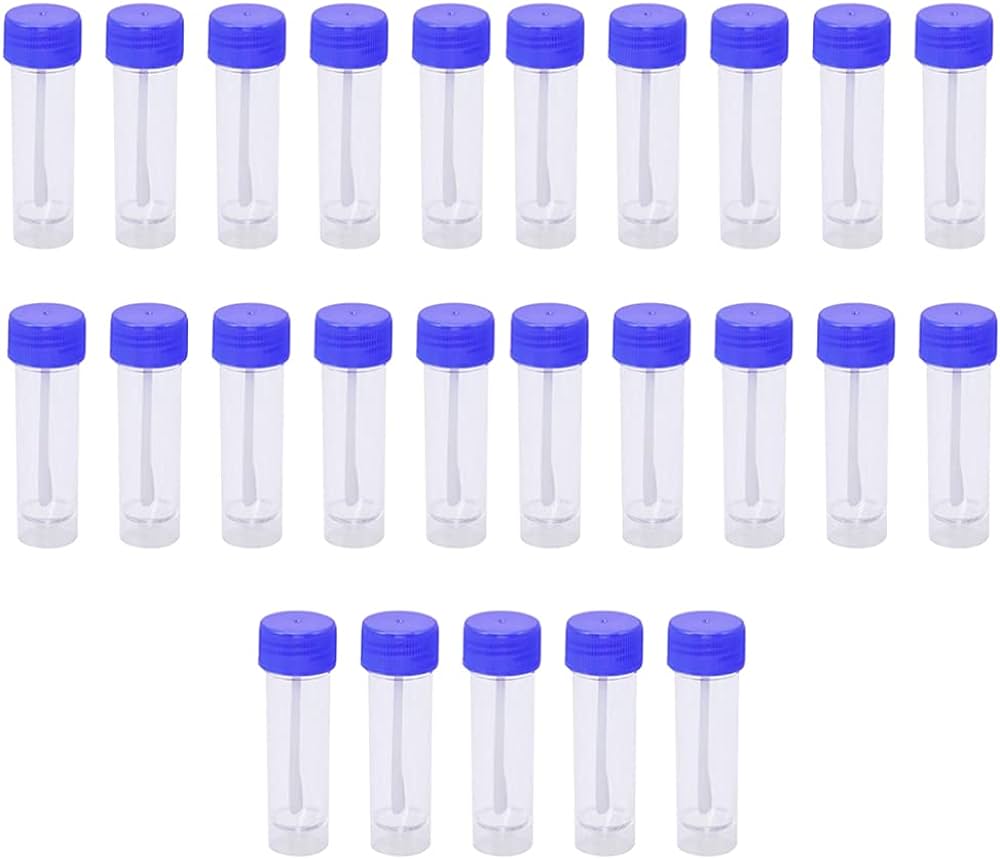
As a consumer, I understand the importance of secure and tamper-proof packaging. When I purchase a product, I want to be confident that it has not been tampered with and that it is safe for consumption or use. Secure packaging ensures that the product remains intact and protected during transportation and storage. It also gives me peace of mind knowing that the manufacturer has taken steps to prevent any contamination or unauthorized access to the product. Tamper-proof packaging plays a crucial role in ensuring the integrity of the product, especially in industries such as food and pharmaceuticals. With tamper-evident seals or packaging features, any attempt to tamper with the product is immediately noticeable, providing an added layer of trust and safety. Overall, secure and tamper-proof packaging is essential in maintaining consumer confidence and safeguarding the quality and safety of products.
3. Types of Capping and Sealing Equipment for Ensuring Product Safety
There are various types of capping and sealing equipment that play a crucial role in ensuring product safety. One of the commonly used equipment is the screw capper. This type of capper is ideal for bottles and containers that require a tight and secure seal. Another type is the induction sealer, which uses heat to bond foil seals onto containers. This ensures that the product remains tamper-proof and prevents any form of contamination. Lastly, we have the crimp capper, which is commonly used in the pharmaceutical industry. This equipment applies pressure to create a tight seal, ensuring product integrity. With the use of these different types of capping and sealing equipment, manufacturers can ensure that their products are safe for consumers to use.
4. Benefits of Implementing Capping and Sealing Equipment in Packaging
As a packaging professional, I have experienced firsthand the benefits of implementing capping and sealing equipment in our packaging process. Firstly, it greatly enhances the efficiency and speed of our production line. With automated capping and sealing machines, we are able to process a higher volume of products in a shorter period of time, saving us both time and money. Secondly, the equipment ensures consistent and accurate sealing, minimizing the risk of leakage or contamination. This is particularly important for perishable or sensitive products, as it maintains their quality and extends their shelf life. Lastly, the use of capping and sealing equipment increases the overall professionalism and reliability of our packaging, instilling trust and confidence in our customers.
5. Best Practices for Choosing and Using Capping and Sealing Equipment
When it comes to choosing and using capping and sealing equipment, there are a few best practices that I always keep in mind. First and foremost, it is crucial to understand the specific needs and requirements of your product. This includes considering factors such as the type of packaging material and the desired level of seal integrity. Additionally, I recommend thoroughly researching different capping and sealing equipment options to ensure compatibility with your production line and volume demands. Regular maintenance and calibration of the equipment are also essential to ensure optimal performance and prevent any downtime. Lastly, training your staff on the proper operation and safety protocols of the equipment is vital to ensure smooth and efficient production processes. By following these best practices, you can ensure that your capping and sealing processes are reliable, efficient, and deliver top-quality results.
6. Overcoming Challenges in Implementing Secure Packaging with Capping and Sealing Equipment
In my experience, implementing secure packaging with capping and sealing equipment has posed various challenges that required careful attention and creative problem-solving. One major hurdle was ensuring the equipment was compatible with the specific packaging materials and sizes we were using. This involved extensive research and testing to find the right equipment that could effectively handle our packaging requirements. Additionally, training our staff on the proper operation and maintenance of the equipment proved to be a challenge, as it required dedicated time and resources. However, by addressing these challenges head-on and implementing strategic solutions, we were able to successfully overcome them and achieve secure and efficient packaging processes.
Conclusion
In conclusion, capping and sealing equipment play a vital role in ensuring secure and tamper-proof packaging. These tools not only protect the integrity of products but also provide peace of mind to consumers. With advancements in technology, capping and sealing equipment continue to evolve, offering more efficient and reliable solutions for packaging needs.
What kind of equipment is used for capping and sealing?
The equipment used for capping and sealing includes capping machines, induction sealers, cap torque testers, and pressure-sensitive label applicators.
What is the purpose of capping and sealing?
The purpose of capping and sealing is to ensure secure and tamper-proof packaging for products, preventing leaks, contamination, and unauthorized access.
How does an induction sealer work?
An induction sealer works by creating a high-frequency electromagnetic field that heats the foil lining on a container’s cap. This causes the foil to bond with the container, creating a hermetic seal.
What is the function of a cap torque tester?
A cap torque tester is used to measure the force required to open or close a cap and ensure it is within the desired torque range. This helps ensure proper sealing and prevents over-tightening or under-tightening.
What are pressure-sensitive label applicators used for?
Pressure-sensitive label applicators are used to automatically apply labels to products or containers. These applicators use pressure to adhere labels firmly to surfaces, ensuring they won’t peel off easily.
Why is secure and tamper-proof packaging important?
Secure and tamper-proof packaging is important to ensure the safety and integrity of products during storage, transportation, and distribution. It helps protect consumers from contaminated or compromised products and also helps build trust in the brand.