Abrasive cutting machines and precision grinding are essential tools in the field of metalwork. These machines play a crucial role in shaping and finishing metal components with accuracy and efficiency. In this article, we will explore the various types of abrasive cutting machines and precision grinding techniques used in metalwork, highlighting their importance and applications in different industries.
Introduction to Abrasive Cutting Machines in Metalwork
Abrasive cutting machines are essential tools in metalwork that are used to cut and shape various types of metal materials. These machines utilize abrasive wheels or discs to remove material from the workpiece, resulting in precise and accurate cuts. They are commonly used in industries such as manufacturing, construction, and automotive, where metal components need to be cut to specific dimensions.
One of the main advantages of abrasive cutting machines is their versatility. They can be used to cut a wide range of metals, including steel, aluminum, and stainless steel. This makes them suitable for various applications, from cutting pipes and bars to shaping intricate metal parts.
In addition to their versatility, abrasive cutting machines are also known for their efficiency. They can make quick and precise cuts, saving time and effort compared to manual cutting methods. This is especially beneficial in industries where large quantities of metal components need to be cut.
Safety is another important aspect of abrasive cutting machines. These machines are equipped with safety features such as guards and emergency stop buttons to prevent accidents and injuries. However, it is still crucial for operators to follow proper safety procedures and wear protective gear when using these machines.
Overall, abrasive cutting machines play a crucial role in metalwork by providing efficient and precise cutting solutions. Their versatility, efficiency, and safety features make them indispensable tools in various industries.
The Importance of Precision Grinding in Metalwork
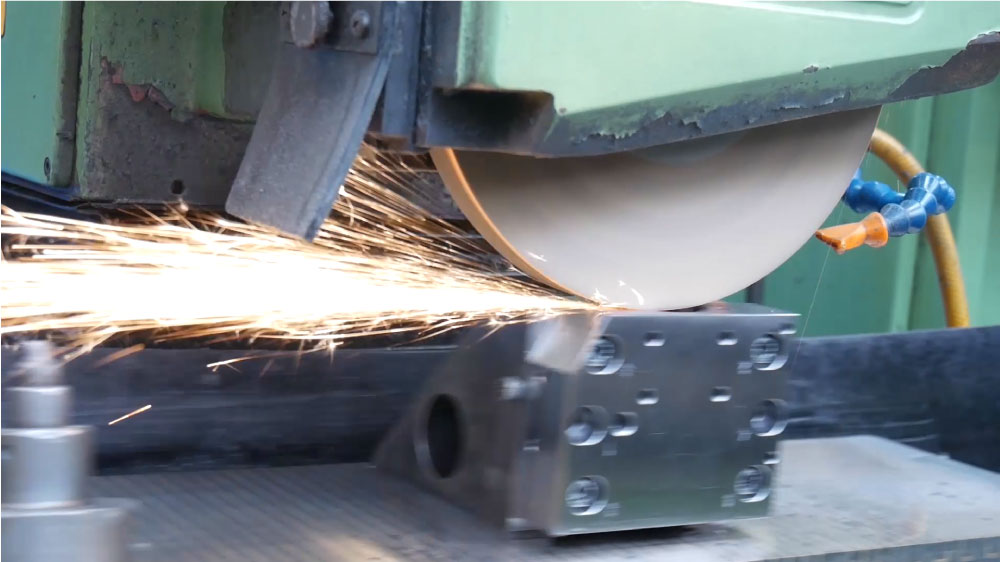
Precision grinding is a crucial process in metalwork that ensures the accuracy and quality of the final product. It involves removing excess material from a workpiece using a grinding wheel, resulting in a smooth and precise finish. This process is essential for various industries, including automotive, aerospace, and manufacturing, as it helps achieve tight tolerances and precise dimensions. Precision grinding also improves the surface finish of the metal, enhancing its appearance and functionality. Additionally, it helps eliminate any imperfections or irregularities in the metal, ensuring its durability and longevity. Overall, precision grinding plays a vital role in metalwork by ensuring the highest level of precision, quality, and performance in the final product.
Types of Abrasive Cutting Machines for Metalwork
There are several types of abrasive cutting machines that are commonly used in metalwork. One of the most popular types is the abrasive chop saw, which is a stationary machine that uses a circular blade with abrasive particles embedded in it to cut through metal. Another common type is the abrasive waterjet cutter, which uses a high-pressure stream of water mixed with abrasive particles to cut through metal. This type of machine is known for its precision and versatility. Additionally, there are abrasive belt grinders, which use a continuous belt with abrasive particles to grind and shape metal. Overall, these machines are essential tools in metalwork and offer various options for cutting and shaping metal materials.
Advantages and Limitations of Precision Grinding in Metalwork
Precision grinding is a highly effective technique used in metalwork that offers several advantages. Firstly, it allows for the production of extremely precise and accurate components, ensuring a high level of quality and consistency. This is particularly important in industries such as aerospace and automotive, where precision is crucial. Additionally, precision grinding can be used to achieve a wide range of surface finishes, from smooth and polished to rough and textured, depending on the specific requirements of the project. However, it is important to note that precision grinding also has its limitations. It can be a time-consuming process, requiring careful setup and adjustment, and it may not be suitable for all types of materials or components.
Safety Measures and Best Practices for Using Abrasive Cutting Machines
When using abrasive cutting machines, it is crucial to prioritize safety measures and follow best practices to prevent accidents and injuries. Firstly, operators should always wear appropriate personal protective equipment (PPE) such as safety glasses, gloves, and ear protection. It is also important to inspect the machine before each use, checking for any damaged or worn-out parts that may affect its performance or safety. Additionally, operators should receive proper training on how to operate the machine safely and be aware of the potential hazards associated with abrasive cutting. Regular maintenance and cleaning of the machine are also essential to ensure its optimal performance and longevity. By adhering to these safety measures and best practices, operators can minimize the risk of accidents and create a safer working environment.
Choosing the Right Abrasive Cutting Machine for Your Metalwork Needs
When it comes to metalwork, choosing the right abrasive cutting machine is crucial. There are several factors to consider before making a decision. Firstly, you need to determine the type of metal you will be working with. Different metals require different cutting techniques and machines. Secondly, consider the size and thickness of the metal. This will determine the power and capacity of the machine you need. Additionally, think about the precision and accuracy required for your project. Some machines offer more precise cutting capabilities than others. Lastly, consider your budget and the long-term maintenance costs of the machine. It’s important to find a machine that fits your needs and budget while also providing reliable performance.
Conclusion
In conclusion, abrasive cutting machines play a crucial role in precision grinding in metalwork. These machines offer a high level of accuracy and efficiency, allowing for the creation of precise and intricate metal parts. With advancements in technology, abrasive cutting machines continue to evolve and improve, making them an essential tool in the metalworking industry.
What are abrasive cutting machines?
Abrasive cutting machines are tools used in metalwork to cut and shape materials using abrasive discs or wheels.
What is precision grinding?
Precision grinding is a process used to remove small amounts of material from a workpiece to achieve a high level of accuracy and smoothness.
What types of materials can be worked on with abrasive cutting machines?
Abrasive cutting machines can be used on a wide range of materials, including metals such as steel, aluminum, and titanium, as well as ceramics, composites, and plastics.
What industries use abrasive cutting machines?
Abrasive cutting machines are commonly used in industries such as automotive, aerospace, manufacturing, and construction.
What are the advantages of using abrasive cutting machines?
Some advantages of using abrasive cutting machines include precise cutting and shaping capabilities, high material removal rates, and the ability to work on a variety of materials.
Are there any safety precautions to consider when using abrasive cutting machines?
Yes, it is important to wear appropriate personal protective equipment, such as safety glasses and gloves, when operating abrasive cutting machines. It is also important to follow proper operating procedures and ensure the machine is properly maintained.