The field of electronics manufacturing involves the production of electronic components and devices. This process requires the use of various materials and involves several intricate processes. In this article, we will explore the different materials and processes used in electronics manufacturing and their impact on the overall quality and functionality of electronic products.
1. Introduction to Electronics Manufacturing Materials and Processes
As an electronics manufacturing professional, I am constantly amazed by the intricate materials and processes that go into creating electronic devices. From smartphones to televisions, a diverse range of components and technologies are employed to produce these cutting-edge products. Electronics manufacturing involves a myriad of materials, such as semiconductors, metals, plastics, and ceramics, each with their unique properties and applications. Furthermore, the processes used in manufacturing are equally fascinating, involving techniques like surface mount technology, printed circuit board assembly, and integrated circuit packaging. In this article, I will delve into the world of electronics manufacturing materials and processes to shed light on the behind-the-scenes work that brings our modern gadgets to life.
2. Key Components and Materials Used in Electronics Manufacturing
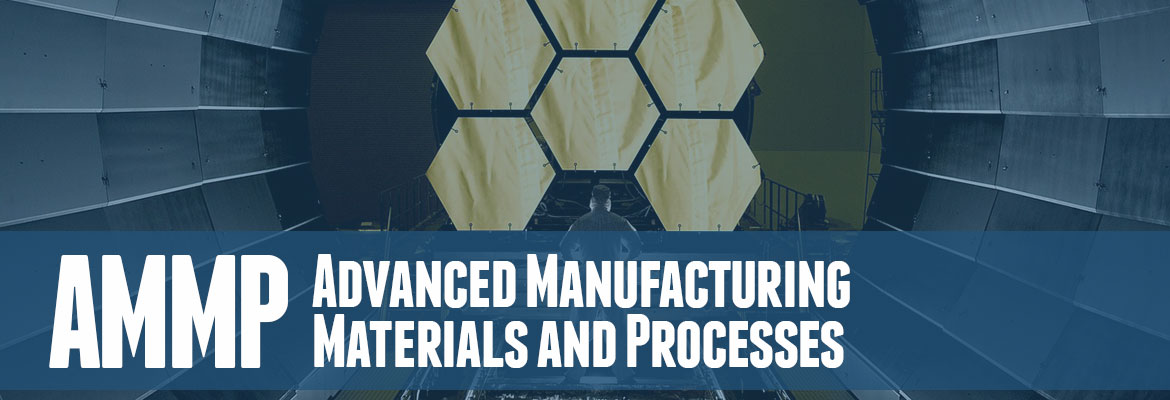
In the world of electronics manufacturing, there are two key components and materials that play a vital role – printed circuit boards (PCBs) and integrated circuits (ICs). PCBs serve as the foundation for electronic devices, providing a platform for all the required components to be interconnected. They are made of a variety of materials such as fiberglass, epoxy, and copper, which allow for conductivity and durability. On the other hand, ICs are the brains of electronic devices, containing thousands or even millions of transistors and other electronic components integrated onto a single chip. These chips are made using materials such as silicon, which has excellent electrical properties. Both PCBs and ICs are essential in the manufacturing process and contribute greatly to the functionality and performance of electronic devices.
3. Understanding the Manufacturing Process for Electronics
Understanding the manufacturing process for electronics is essential for anyone working in the electrical engineering field. As a female electrical engineer, I have gained valuable insights into this intricate process. From the initial design phase to the final assembly, it is crucial to have a thorough understanding of each step in order to ensure quality and efficient production. This includes familiarizing oneself with the various materials, tools, and technologies used in electronic manufacturing. Additionally, staying updated with the latest advancements in the industry is key to staying competitive in today’s fast-paced world. By continually educating myself and refining my knowledge in this area, I am able to contribute effectively to the manufacturing process and drive innovation in the field.
4. Challenges and Advances in Electronics Manufacturing Materials
As a woman working in the electronics manufacturing industry, I have experienced firsthand the challenges and advances in materials used in our field. One of the biggest challenges we face is keeping up with the constant evolution of technology. With each new generation of electronics, we are required to find new materials that can meet the increasing demands for efficiency and performance. This means constantly researching and testing different materials to find the best fit for our products. However, this challenge also brings opportunities for advancement. We have seen great strides in the development of innovative materials such as graphene and nanomaterials, which have revolutionized the electronics manufacturing industry. These materials offer improved conductivity, flexibility, and durability, allowing us to create smaller and more powerful devices. Despite the challenges we face, it is exciting to be a part of an industry that is constantly pushing the boundaries of what is possible in electronics manufacturing.
5. Quality Control and Testing Methods for Electronics Manufacturing
Quality control and testing methods are vital in the manufacturing of electronics. As a manufacturer, I understand the importance of ensuring that the products we produce meet the highest standards of quality and safety. This involves rigorous testing at various stages of the manufacturing process, from the initial design phase to the final production. We employ a combination of manual and automated testing methods to ensure accuracy and reliability of our products. Quality control measures include visual inspection, component testing, and performance testing to ensure that our electronics meet the specifications and standards set by regulatory bodies. By implementing these methods, we can confidently deliver high-quality products to our customers, enhancing their trust in our brand.
6. Future Trends in Electronics Manufacturing Materials and Processes
As an engineer working in the electronics manufacturing industry, I am excited about the future trends that will shape the materials and processes we use. One of the most significant developments I foresee is the increasing use of nanomaterials in electronic devices. These tiny materials have unique properties at the nanoscale, which can greatly enhance the performance and efficiency of electronic components. Additionally, I expect to see a shift towards more sustainable manufacturing processes. With the growing concern for the environment, manufacturers are becoming more mindful of their impact and are adopting greener practices. This includes utilizing renewable energy sources and recycling materials to reduce waste. Overall, I believe the future of electronics manufacturing will be characterized by innovation, efficiency, and environmental consciousness.
Conclusion
In conclusion, electronics manufacturing materials and processes play a crucial role in the development and production of electronic devices. These materials and processes need to be carefully selected and implemented to ensure the quality, reliability, and performance of the final products. As technology continues to advance, it is important for manufacturers to stay updated on the latest materials and processes to remain competitive in the industry.
Question 1: What are the common materials used in electronics manufacturing?
Common materials used in electronics manufacturing include semiconductors, conductive materials, insulators, resistors, capacitors, inductors, and various types of connectors and cables.
Question 2: What processes are involved in electronics manufacturing?
Electronics manufacturing involves several processes such as printed circuit board (PCB) design and fabrication, surface mount technology (SMT), soldering, component assembly, testing, and quality control.
Question 3: How are printed circuit boards manufactured?
Printed circuit boards (PCBs) are typically manufactured using a subtractive process. This involves starting with a copper-clad laminate, applying a photosensitive material, exposing it to a patterned artwork, developing it to remove unwanted copper, and finally etching the remaining copper to form the desired circuit traces.
Question 4: What is surface mount technology (SMT)?
Surface mount technology (SMT) is a method of assembling electronic components on the surface of a PCB. It involves placing components directly onto the PCB and soldering them using reflow or wave soldering techniques, eliminating the need for drilling holes and inserting components through the board.
Question 5: How are electronic components soldered onto PCBs?
Electronic components are soldered onto PCBs using various methods such as reflow soldering and wave soldering. Reflow soldering involves applying solder paste to the PCB, placing the components onto the paste, and then heating the assembly to melt the solder and create the electrical and mechanical connections. Wave soldering, on the other hand, involves passing the PCB over a wave of molten solder to solder the components.
Question 6: What is the purpose of testing and quality control in electronics manufacturing?
Testing and quality control are crucial in electronics manufacturing to ensure that the final products meet the required standards and specifications. This involves performing functional tests, electrical testing, visual inspections, and reliability testing to identify any faults or defects and ensure the overall quality of the manufactured electronics.