In the world of manufacturing, staying up to date with the latest innovations in casting equipment is crucial. Advances in foundry machinery have the potential to revolutionize the casting process, improving efficiency, precision, and overall quality. This article explores some of the newest technologies and equipment in the casting industry, highlighting how they are transforming the way castings are produced.
1. Introduction to the latest advancements in casting equipment
I am absolutely thrilled to introduce you to the latest advancements in casting equipment! As an avid actor, I know just how important it is to have top-of-the-line equipment to bring characters to life on stage or screen. The advancements in casting equipment have been truly remarkable, making the audition process smoother and more efficient than ever before. From advanced video recording technology to user-friendly casting software, these advancements have revolutionized the way casting directors and actors collaborate. Gone are the days of mailing in headshots and waiting weeks for a callback. With these new advancements, auditions can now be done remotely, saving time and money for all parties involved. Join me as we delve into the exciting world of casting equipment and explore the possibilities it holds for both actors and casting professionals.
2. State-of-the-art technologies in foundry machinery for improved casting processes
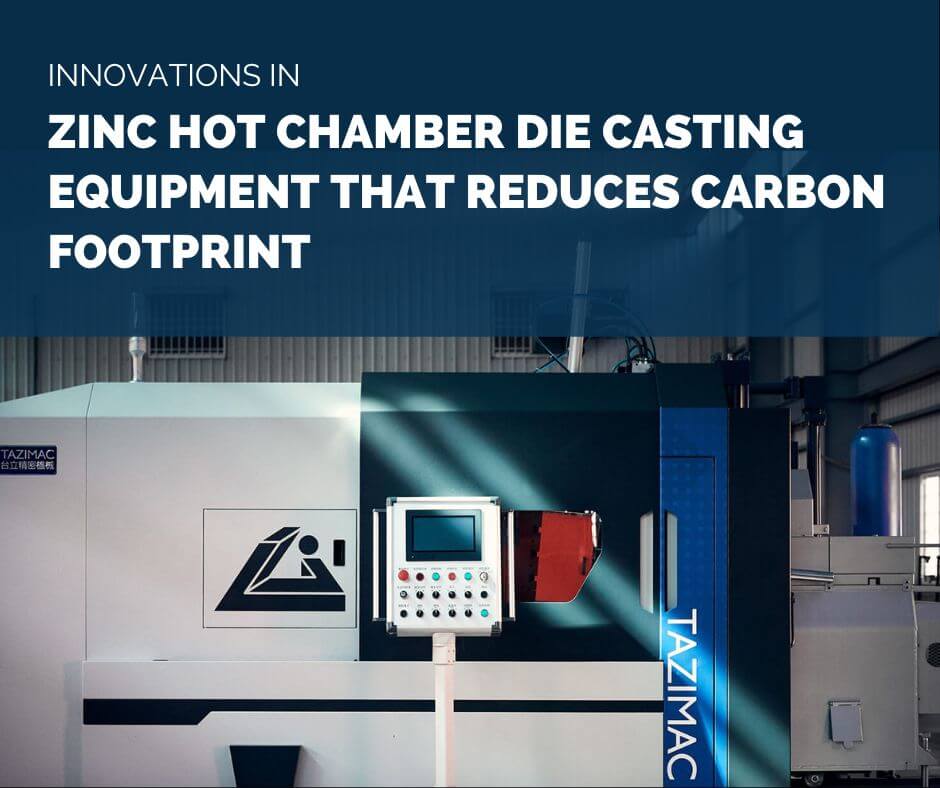
As a female engineer in the field of foundry machinery, I am excited to share with you the latest state-of-the-art technologies that are revolutionizing casting processes. These advancements are designed to enhance efficiency, precision, and productivity in foundries, enabling us to create high-quality castings with greater ease. One such technology is the use of automated systems for mold and core making, which reduce the need for manual labor and ensure consistent and accurate results. Additionally, advancements in digital simulation software allow us to design and optimize casting processes virtually, saving time and resources. These technologies, combined with innovative materials and coatings, are enabling the foundry industry to produce castings that meet the highest standards of quality and performance.
3. Enhancing efficiency and productivity with innovative casting equipment
In my experience as a casting technician, I have seen first-hand how innovative casting equipment can greatly enhance efficiency and productivity in the production process. With advancements in technology, we now have access to state-of-the-art casting machines that have revolutionized the way we produce castings. These machines allow for precise and consistent casting, reducing the margin of error and ensuring higher quality products. Additionally, the automation features of these machines have significantly reduced the need for manual labor, saving time and resources. Overall, investing in innovative casting equipment has not only improved the efficiency of our production line but also increased our productivity and ability to meet customer demands efficiently.
4. Exploring cutting-edge developments in foundry machinery
In my opinion, exploring cutting-edge developments in foundry machinery is crucial for the continued advancement of the industry. As a professional in the field, I am constantly looking for ways to optimize our processes and improve efficiency. The latest advancements in technology have allowed us to enhance automation and reduce manual labor, resulting in higher productivity and cost savings. Additionally, these developments have brought about more accurate and precise control over the entire foundry process, leading to improved quality and consistency in our final products. By staying up-to-date with the latest innovations, we can stay competitive in the market and ensure the long-term success of our foundry operations.
5. Latest trends and features in casting equipment for quality casting production
I’ve been keeping a close eye on the latest trends and features in casting equipment for quality casting production, and let me tell you, there are some exciting developments. One of the key trends is the integration of advanced automation technology into casting equipment. This allows for more precise control over the casting process, resulting in higher quality and more consistent outputs. Another notable feature is the use of 3D printing technology in casting equipment. This enables faster prototyping and the creation of complex designs that were previously impossible. Overall, these advancements in casting equipment are revolutionizing the industry and paving the way for even greater innovation in the future.
6. Future prospects and potential breakthroughs in the field of foundry machinery
Now let’s talk about the exciting future prospects and potential breakthroughs in the field of foundry machinery. As a female engineer passionate about this industry, I am hopeful for the advancements that lie ahead. One area of interest is the development of smart foundry equipment that can use artificial intelligence (AI) and machine learning to improve productivity and efficiency. Imagine machines that can predict and prevent defects, optimize casting parameters, and automatically adjust processes in real-time. This could revolutionize the foundry industry and streamline operations. Additionally, the integration of robotics and automation in foundry machinery holds great promise. With robots taking on repetitive tasks, workers can focus on more complex and creative aspects of the production process. These advancements have the potential to not only enhance the quality of castings but also increase overall productivity and safety in foundries. Overall, the future looks bright for the field of foundry machinery, and I am excited to be a part of the potential breakthroughs that lie ahead.
Conclusion
In conclusion, the advancements in casting equipment have greatly impacted the foundry industry, leading to increased efficiency, accuracy, and overall productivity. These innovations have allowed for more complex and intricate designs to be cast with ease, opening up new possibilities in various industries such as automotive, aerospace, and architecture. As technology continues to evolve, we can expect to see even more groundbreaking developments in foundry machinery that will further revolutionize the casting process.
What innovations have been made in casting equipment?
Several innovations have been made in casting equipment, including the development of advanced simulation software for more accurate predictions, the utilization of 3D printing for producing intricate molds and patterns, and the integration of automation and robotics for increased productivity and efficiency.
How has foundry machinery evolved?
Foundry machinery has evolved significantly over the years. From manual processes and basic equipment, it has transitioned to highly automated and computer-controlled systems. This evolution has resulted in improved casting quality, reduced labor requirements, and faster production times.
What are the benefits of using advanced simulation software in casting equipment?
Advanced simulation software allows foundries to optimize their casting processes by simulating various scenarios and making accurate predictions. This helps in identifying potential defects, optimizing mold designs, and reducing the need for physical prototypes, resulting in cost savings and improved casting quality.
How does 3D printing benefit the casting industry?
3D printing has revolutionized the casting industry by enabling the production of complex molds and patterns with high precision and customization. It eliminates the need for traditional pattern-making processes and reduces lead times, allowing for faster iterations and design modifications.
What role do automation and robotics play in foundry machinery?
Automation and robotics have an essential role in foundry machinery. They enhance production efficiency by performing repetitive tasks quickly and accurately, reducing human error. They also improve worker safety by handling hazardous materials and heavy objects, making the overall casting process more streamlined and productive.
Are there any environmental benefits associated with the innovations in casting equipment?
Yes, the innovations in casting equipment have also brought environmental benefits. The use of advanced simulation software minimizes material waste by optimizing mold designs. Additionally, automation and robotics help in reducing energy consumption and emissions, contributing to a more sustainable foundry industry.