Plasma cutting machines have revolutionized the metal cutting industry with their ability to cut through various materials with precision and speed. These machines use a high-temperature plasma arc to melt and sever metal, resulting in clean and accurate cuts. In this article, we will explore the benefits and applications of plasma cutting machines and how they have transformed the hot cutting process.
Introduction to Plasma Cutting Machines: A Revolutionary Hot Cutting Technique
Plasma Cutting Work (Plasma Cutting Torch and Plasma Cutting Machine)
plasmacutter #plasmacutting #plasmacuttingmachine.
Plasma cutting machines have revolutionized the hot cutting technique by offering a more efficient and precise method for cutting various materials. These machines use a high-velocity jet of ionized gas, known as plasma, to melt and sever through metals and other conductive materials. The plasma is created by passing an electric current through a gas, typically compressed air, and then directing it towards the material to be cut. This process allows for a clean and accurate cut, with minimal heat-affected zones and distortion. Plasma cutting machines are widely used in industries such as automotive, construction, and manufacturing, where precision and speed are crucial.
How Plasma Cutting Machines Work: Understanding the Precision Behind the Process
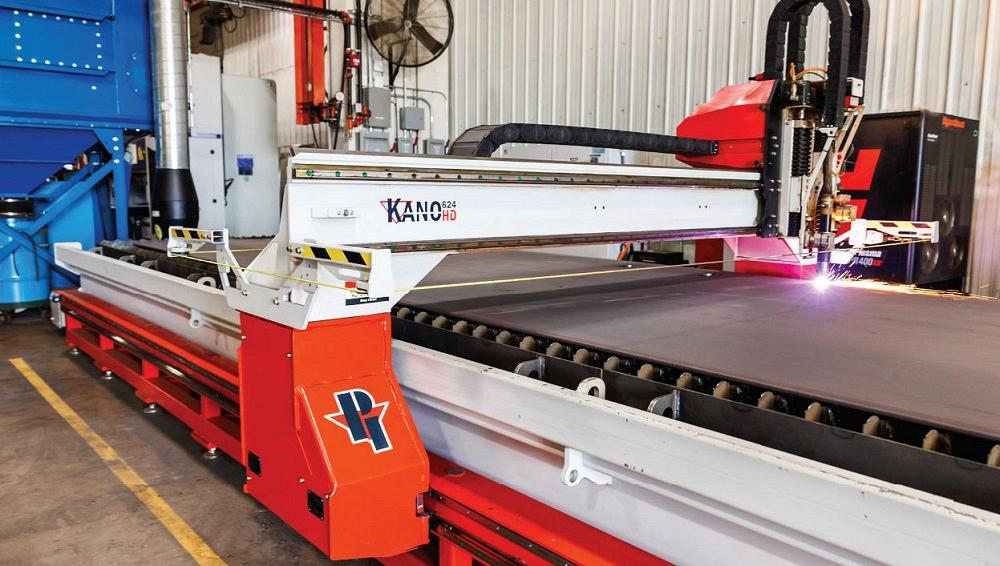
Plasma cutting machines are a vital tool in various industries, including metal fabrication and automotive manufacturing. These machines work by utilizing a high-velocity jet of ionized gas, known as plasma, to cut through different types of materials with precision and accuracy. The process begins with the creation of an electrical circuit, which generates a powerful electric arc between the electrode and the workpiece. This arc heats the gas, transforming it into plasma. The plasma, with its extremely high temperature, melts the material being cut, while a high-velocity gas jet blows away the molten metal, creating a clean and precise cut. This efficient and versatile cutting method has revolutionized the manufacturing industry, allowing for faster production times and improved quality of finished products.
Advantages of Plasma Cutting Machines: Why They’re the Preferred Choice for Hot Cutting
Plasma cutting machines have become the preferred choice for hot cutting due to their numerous advantages. Firstly, these machines offer high precision and accuracy, allowing for clean and smooth cuts. This is especially important in industries such as metal fabrication, where precision is crucial. Additionally, plasma cutting machines are highly versatile and can cut through a wide range of materials, including steel, aluminum, and stainless steel. This makes them suitable for various applications in industries such as automotive, aerospace, and construction. Furthermore, plasma cutting machines are known for their speed and efficiency, enabling faster production and reducing overall project time. Overall, the advantages of plasma cutting machines make them a valuable tool for any hot cutting needs.
Applications of Plasma Cutting Machines: Exploring the Versatility of this Cutting Technique
Plasma cutting machines have become increasingly popular in various industries due to their versatility and efficiency. One of the main applications of these machines is in the metal fabrication industry, where they are used to cut through various types of metals with precision and speed. This cutting technique is also commonly used in the automotive industry for cutting and shaping metal parts. Additionally, plasma cutting machines are utilized in the construction industry for cutting metal sheets and beams. Another emerging application of plasma cutting machines is in the art and design industry, where they are used to create intricate and detailed metal sculptures. Overall, the versatility of plasma cutting machines makes them a valuable tool in a wide range of industries.
Factors to Consider When Choosing a Plasma Cutting Machine: Finding the Perfect Fit for Your Needs
When choosing a plasma cutting machine, there are several factors that need to be considered in order to find the perfect fit for your needs. Firstly, it is important to determine the thickness of the materials you will be cutting. Different machines have different cutting capacities, so it is crucial to choose one that can handle the thickness of your materials. Secondly, consider the size of the machine and the space you have available in your workshop. It is important to choose a machine that will fit comfortably in your workspace. Additionally, consider the power source and the type of plasma cutter you need. Some machines require a specific power source, so make sure you have the necessary infrastructure in place. Lastly, consider your budget and the cost of the machine. It is important to find a machine that fits within your budget while still meeting your needs. By considering these factors, you can find the perfect plasma cutting machine for your needs.
Maintenance and Safety Tips for Plasma Cutting Machines: Ensuring Longevity and Protection
When it comes to plasma cutting machines, proper maintenance and safety measures are crucial for ensuring their longevity and protecting both the machine and the operator. Regularly inspecting and cleaning the machine, as well as checking for any loose or damaged parts, is essential. It is also important to follow the manufacturer’s guidelines for maintenance and to use the recommended consumables. Safety precautions such as wearing protective gear, ensuring proper ventilation, and keeping a fire extinguisher nearby are necessary to prevent accidents. By taking these maintenance and safety tips into consideration, plasma cutting machines can continue to operate efficiently and safely for a long time.
Conclusion
In conclusion, plasma cutting machines offer a highly efficient and precise method of cutting various materials. With their ability to generate intense heat, these machines can easily cut through thick metals and other tough materials. Whether used in industrial settings or for personal projects, plasma cutting machines are a valuable tool for achieving accurate and clean cuts.
What is plasma cutting?
Plasma cutting is a process that uses a high-velocity jet of ionized gas, known as plasma, to cut through electrically conductive materials.
What materials can be cut using plasma cutting?
Plasma cutting can be used to cut a wide range of electrically conductive materials, including steel, stainless steel, aluminum, copper, and brass.
How does plasma cutting work?
Plasma cutting works by sending an electric arc through a gas that is passing through a constricted opening. This creates a plasma jet that can reach temperatures of up to 30,000 degrees Fahrenheit, melting the material and blowing away the molten metal.
What are the advantages of plasma cutting?
Plasma cutting offers several advantages, including high cutting speeds, precision cutting with minimal heat-affected zones, and the ability to cut through thick materials.
Are there any limitations to plasma cutting?
While plasma cutting is a versatile cutting method, it does have some limitations. It is not suitable for cutting non-conductive materials, such as wood or plastic, and it may produce some dross or slag on the cut edges.
What industries use plasma cutting machines?
Plasma cutting machines are widely used in industries such as automotive, aerospace, construction, metal fabrication, and shipbuilding, among others.