Specialty chemicals play a crucial role in various industries such as pharmaceuticals, cosmetics, and electronics. The process of mixing and blending these chemicals is essential for achieving desired product characteristics and quality. This article explores the importance of mixing and blending techniques in the production of specialty chemicals and highlights the key factors to consider for optimal results.
1. The Importance of Mixing and Blending in Specialty Chemicals Production
As a chemist working in the specialty chemicals industry, I cannot stress enough the importance of mixing and blending in our production processes. Mixing and blending are crucial steps in creating high-quality and consistent specialty chemicals. These processes allow us to combine different compounds and ingredients together, ensuring their effective integration and resulting in a homogenous final product. By carefully controlling the mixing and blending parameters, we can optimize the efficiency and performance of our chemicals. Additionally, proper mixing and blending techniques contribute to the overall safety and stability of our production processes. Neglecting or overlooking these steps can lead to inferior products, inconsistent batch-to-batch quality, and potential hazards. Thus, as a chemist, I always prioritize and emphasize the significance of mixing and blending in specialty chemicals production.
2. Understanding the Role of Mixing and Blending Equipment in the Specialty Chemicals Industry
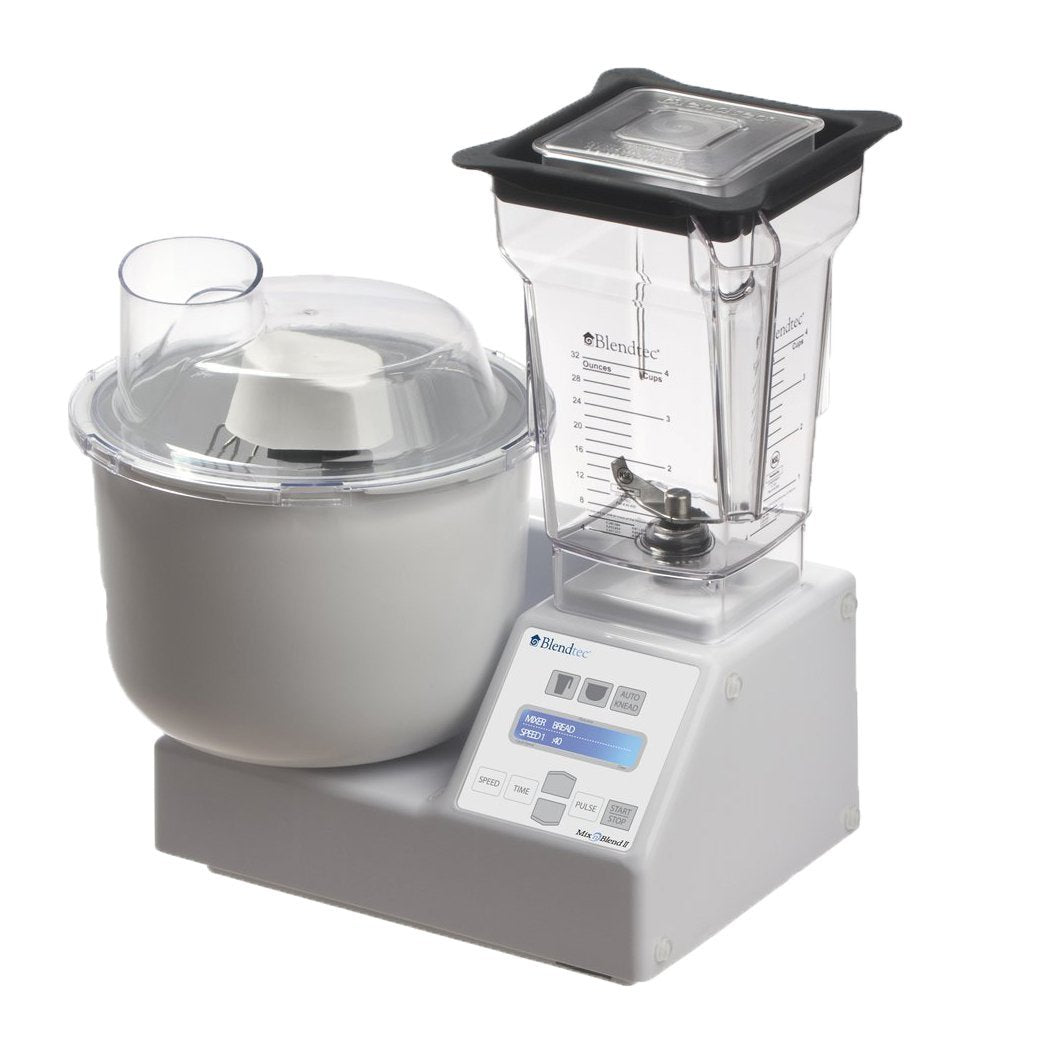
When it comes to the specialty chemicals industry, the role of mixing and blending equipment cannot be overstated. As someone who has worked in this industry for many years, I have witnessed firsthand the importance of having reliable and efficient equipment for the production of specialty chemicals. Whether it is dyes, pharmaceuticals, or fragrances, the quality of the final product is highly dependent on the mixing and blending processes. This is why investing in high-quality equipment is crucial. It ensures that the ingredients are thoroughly mixed, creating a uniform and consistent product. Additionally, good equipment helps in achieving the desired chemical reactions and ensures that the process is carried out safely and efficiently. In a highly competitive industry like ours, having the right mixing and blending equipment can give us the edge we need to stay ahead of the competition and meet the ever-increasing demands of our customers.
3. Key Factors to Consider for Optimal Mixing and Blending of Specialty Chemicals
When it comes to the optimal mixing and blending of specialty chemicals, there are three key factors that should be considered. First and foremost, it is important to understand the chemical composition and properties of the substances that are being mixed together. This knowledge will help determine the appropriate temperature, pressure, and mixing speed for achieving the desired outcome. Secondly, the equipment used for mixing and blending plays a crucial role in the process. It is essential to have high-quality and well-maintained equipment that is capable of providing consistent results. Finally, the expertise and experience of the person handling the mixing and blending process are vital. This individual should have a deep understanding of the chemicals being used and the technical skills to operate the equipment effectively. By considering these key factors, optimal mixing and blending of specialty chemicals can be achieved, resulting in high-quality products.
4. Innovative Technologies for Efficient Mixing and Blending in Specialty Chemicals
Innovative technologies have revolutionized the mixing and blending processes in the specialty chemicals industry. As a professional in this field, I have witnessed the remarkable improvements these technologies have brought to our daily operations. These advancements have not only increased efficiency but have also enhanced the quality and consistency of our products. The introduction of automated systems and robotics has eliminated the need for manual labor, reducing the risk of human error and ensuring precise measurements and ratios. Furthermore, the integration of artificial intelligence and machine learning has allowed for real-time monitoring and adjustment of the blending process, resulting in faster production times and reduced wastage. Overall, these innovative technologies have undoubtedly propelled the specialty chemicals industry forward, making our work more efficient and our products even better.
5. Challenges and Solutions in Mixing and Blending Specialty Chemicals
As a specialist in mixing and blending specialty chemicals, I have come across various challenges in my career. One major challenge is ensuring the compatibility of different chemicals that need to be mixed together. Each chemical may have different physical and chemical properties, which can make it difficult to achieve a homogenous blend. To overcome this, thorough testing and understanding of the chemicals’ characteristics is crucial. Another challenge is maintaining the quality and consistency of the blended product. It requires precise measurements, proper equipment calibration, and an understanding of the desired end result. Additionally, ensuring the safety and handling of hazardous chemicals poses another challenge. Adequate training, protective gear, and adherence to safety protocols are necessary to mitigate any potential risks. Overall, by being knowledgeable, meticulous, and safety-oriented, these challenges can be successfully addressed, ensuring high-quality specialty chemical blends.
6. Best Practices for Achieving Consistency and Quality in Specialty Chemicals Mixing and Blending
When it comes to achieving consistency and high quality in specialty chemicals mixing and blending, there are a few best practices that I have found to be effective. Firstly, it is crucial to thoroughly understand the properties and characteristics of the chemicals being used. This includes their compatibility, stability, and reactivity with other substances. Additionally, proper equipment selection and maintenance are key factors in ensuring accuracy and precision in the mixing process. Regular calibration of instruments and routine cleaning of the equipment can greatly impact the quality of the final product. Finally, implementing strict quality control measures, such as batch testing and documentation, can help identify any variations or deviations in the final product and allow for necessary adjustments. By following these best practices, consistency and quality can be achieved in specialty chemicals mixing and blending.
Conclusion
In conclusion, mixing and blending processes play a crucial role in the production of specialty chemicals. These processes ensure that ingredients are properly combined and distributed, resulting in a final product that meets specific requirements and standards. By employing innovative techniques and equipment, manufacturers can enhance the efficiency and effectiveness of mixing and blending, ultimately contributing to the overall success and quality of specialty chemical production.
What is mixing and blending for specialty chemicals?
Mixing and blending for specialty chemicals involves combining different chemicals or substances to create a customized product with specific properties, composition, or performance. It is often used in industries such as pharmaceuticals, cosmetics, and personal care products.
Why is mixing and blending important for specialty chemicals?
Mixing and blending is important for specialty chemicals to achieve desired product characteristics, ensure uniform distribution of ingredients, and enhance the overall quality of the final product. It allows manufacturers to create unique formulations tailored to meet specific customer requirements.
What equipment is used for mixing and blending specialty chemicals?
Various types of equipment can be used for mixing and blending specialty chemicals, including tanks, agitators, mixers, blenders, and homogenizers. The choice of equipment depends on factors such as the volume of production, the type and viscosity of the chemicals, and the desired level of mixing intensity.
What are the challenges in mixing and blending specialty chemicals?
Some challenges in mixing and blending specialty chemicals include achieving consistent product quality, ensuring thorough mixing of ingredients, minimizing batch-to-batch variations, and maintaining the stability and integrity of sensitive chemical compounds. Additionally, factors such as heat transfer, shear stress, and reaction kinetics need to be carefully considered during the mixing process.
How is the effectiveness of mixing and blending specialty chemicals assessed?
The effectiveness of mixing and blending specialty chemicals can be assessed through various methods, including visual examination, physical testing, and chemical analysis. These techniques help evaluate attributes such as color, texture, viscosity, homogeneity, stability, and performance to ensure that the desired quality standards are met.
Are there any safety precautions to consider when mixing and blending specialty chemicals?
Yes, there are various safety precautions to consider when mixing and blending specialty chemicals. These may include wearing appropriate personal protective equipment (PPE), working in a well-ventilated area, following proper handling and storage procedures for hazardous chemicals, and adhering to industry-specific safety regulations to minimize the risk of accidents or exposure to harmful substances.