Plasma cutting machines have revolutionized the metalwork industry with their high-temperature precision. These machines use a jet of ionized gas to cut through various types of metals with incredible accuracy and speed. From industrial fabrication to artistic creations, plasma cutting machines have become an essential tool for professionals in the metalwork field.
Introduction to Plasma Cutting Machines: A Game-Changer in Metalwork
Plasma cutting machines have revolutionized the metalwork industry with their efficiency and precision. These machines use a high-velocity jet of ionized gas, known as plasma, to cut through various types of metal with ease. Unlike traditional cutting methods, plasma cutting machines can handle a wide range of materials, including stainless steel, aluminum, and copper. This versatility makes them a game-changer in the metalwork field, as they eliminate the need for multiple tools and processes. Additionally, plasma cutting machines offer faster cutting speeds and produce cleaner, more accurate cuts, resulting in higher productivity and cost savings for metalworkers. With their advanced technology and numerous benefits, plasma cutting machines have become an essential tool for any metalwork project.
Understanding the High-Temperature Precision of Plasma Cutting Machines
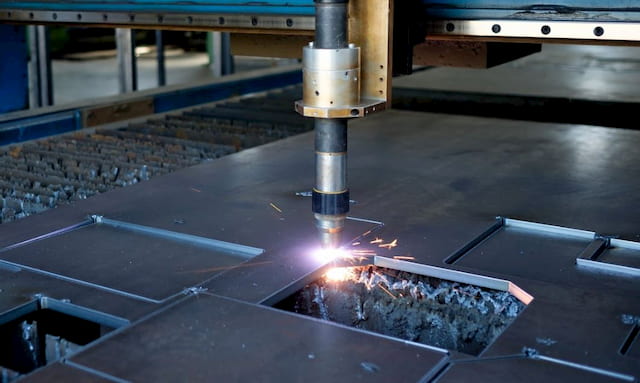
Plasma cutting machines are known for their high-temperature precision, making them a popular choice in various industries. These machines use a high-velocity jet of ionized gas, known as plasma, to cut through different types of materials with extreme accuracy. The high-temperature precision of plasma cutting machines is achieved through the controlled application of heat, which allows for clean and precise cuts. This precision is crucial in industries such as automotive, aerospace, and metal fabrication, where accuracy is paramount. With the ability to cut through thick materials and produce intricate designs, plasma cutting machines have revolutionized the manufacturing process and continue to be a valuable tool in many industries.
Benefits of Using Plasma Cutting Machines in Metalwork
Plasma cutting machines have revolutionized the metalwork industry with their numerous benefits. Firstly, these machines offer exceptional precision and accuracy, allowing for intricate and detailed cuts. This level of precision ensures minimal material wastage, resulting in cost savings for businesses. Additionally, plasma cutting machines are incredibly versatile, capable of cutting through a wide range of metals, including stainless steel, aluminum, and copper. This versatility makes them an essential tool for metalworkers who deal with various materials. Furthermore, plasma cutting machines are known for their speed and efficiency, enabling metalworkers to complete projects in a timely manner. Overall, the benefits of using plasma cutting machines in metalwork are undeniable, making them a valuable asset for any metalworking business.
Factors to Consider When Choosing a Plasma Cutting Machine for High-Temperature Precision
When choosing a plasma cutting machine for high-temperature precision, there are several factors that need to be considered. Firstly, the power source of the machine is crucial. It should be able to provide enough power to cut through thick materials without compromising the precision. Secondly, the cutting speed is important as it determines the efficiency of the machine. A faster cutting speed will save time and increase productivity. Additionally, the machine should have a reliable cooling system to prevent overheating during high-temperature cutting. Lastly, the accuracy and precision of the machine should be top-notch to ensure clean and precise cuts. Considering these factors will help in selecting the right plasma cutting machine for high-temperature precision.
Tips and Techniques for Achieving Optimal Results with Plasma Cutting Machines
Plasma cutting machines are powerful tools that can deliver optimal results when used correctly. To achieve the best outcomes, there are several tips and techniques that can be employed. Firstly, it is important to choose the right plasma cutter for the job. Different machines have varying power levels and cutting capacities, so selecting the appropriate one is crucial. Additionally, ensuring that the machine is properly calibrated and maintained is essential for optimal performance. This includes regularly checking and replacing consumables such as electrodes and nozzles. Furthermore, adjusting the cutting speed and amperage settings can greatly impact the quality of the cut. Finally, practicing proper cutting techniques, such as maintaining a consistent distance between the torch and the workpiece, can help achieve precise and clean cuts. By following these tips and techniques, users can maximize the potential of their plasma cutting machines and achieve optimal results.
Future Innovations in Plasma Cutting Machines for Enhanced High-Temperature Precision
Plasma cutting machines have come a long way in terms of precision and efficiency, but the future holds even more exciting innovations. One area of focus is enhancing high-temperature precision. Researchers are working on developing advanced cooling systems that can handle the extreme heat generated during plasma cutting. This will not only improve the accuracy of the cuts but also increase the lifespan of the machine. Additionally, there is a growing interest in integrating artificial intelligence (AI) into plasma cutting machines. AI algorithms can analyze data in real-time and make adjustments to optimize the cutting process. This will result in faster and more precise cuts, saving time and resources. Overall, the future of plasma cutting machines looks promising, with advancements that will revolutionize the industry.
Conclusion
In conclusion, plasma cutting machines offer high-temperature precision in metalwork, making them a valuable tool for various industries. These machines are capable of cutting through a wide range of materials with ease and accuracy, resulting in clean and precise cuts. With their advanced technology and versatility, plasma cutting machines are a must-have for any metalworking professional.
What is a plasma cutting machine?
A plasma cutting machine is a tool used in metalwork to cut through various types of metal using a high-temperature plasma arc.
How does a plasma cutting machine work?
A plasma cutting machine works by sending an electric arc through a gas that is passing through a constricted opening. This creates a plasma jet that can reach temperatures of up to 30,000 degrees Fahrenheit. The plasma jet melts the metal and blows away the molten material, resulting in a clean and precise cut.
What types of metals can be cut with a plasma cutting machine?
A plasma cutting machine can cut through a wide range of metals, including steel, stainless steel, aluminum, copper, brass, and more.
What are the advantages of using a plasma cutting machine?
Some advantages of using a plasma cutting machine include its ability to cut through thick metals, its high cutting speed, its precision, and its versatility in cutting various types of metals.
Are there any limitations to using a plasma cutting machine?
While plasma cutting machines are highly effective, they do have some limitations. For example, they may not be suitable for cutting materials that are highly reflective, such as aluminum or copper, as the plasma arc can be easily deflected. Additionally, plasma cutting machines may produce a heat-affected zone (HAZ) around the cut, which can affect the material’s properties.
What safety precautions should be taken when using a plasma cutting machine?
When using a plasma cutting machine, it is important to wear appropriate personal protective equipment (PPE), such as safety glasses, gloves, and a welding helmet. It is also important to ensure proper ventilation in the workspace to prevent the buildup of fumes and gases. Additionally, operators should be trained on the safe operation of the machine and follow all manufacturer guidelines and recommendations.