Textile testing equipment plays a crucial role in ensuring the quality and safety of textiles. With the increasing demand for textiles in various industries, it is essential to have reliable and accurate testing equipment to meet the quality standards. This article explores the importance of quality assurance in textiles and the role of testing equipment in achieving it.
Importance of Quality Assurance in Textile Testing Equipment
Textile Testing Process yarn/gsm/pilling
RR LAB 2 sastri Nagar , 2 nd Street, angeripalayam road tiruppur-641602 0421-4540103 connect: VENKATESH mobile : 98422 ...
Quality assurance plays a crucial role in the textile industry, especially when it comes to testing equipment. Textile testing equipment is used to ensure that the fabrics and materials used in the production process meet the required standards and specifications. Without proper quality assurance measures in place, there is a risk of producing substandard products that may not meet customer expectations or regulatory requirements. Quality assurance in textile testing equipment involves regular calibration and maintenance of the equipment, as well as conducting thorough and accurate testing procedures. This helps to identify any potential issues or defects early on, allowing for timely corrective actions to be taken. Ultimately, quality assurance in textile testing equipment helps to ensure the production of high-quality and reliable textile products.
Key Parameters for Ensuring Quality in Textile Testing Equipment
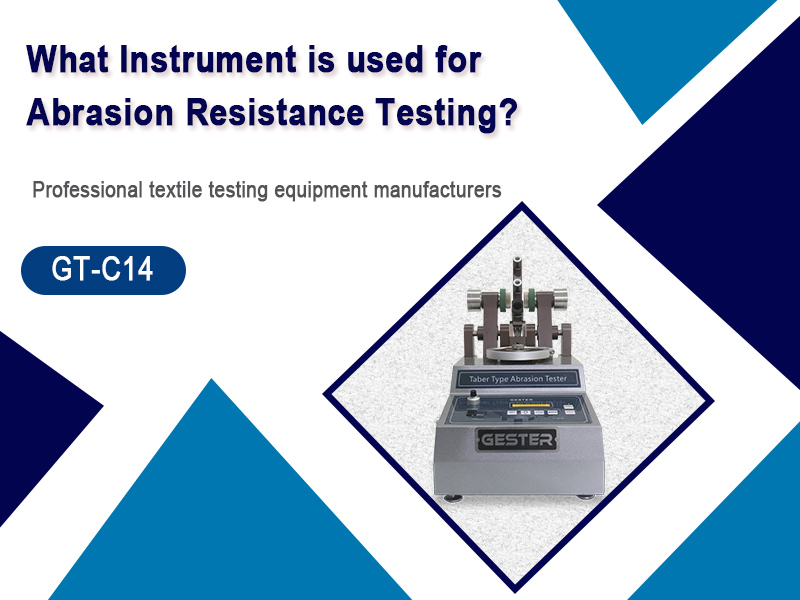
When it comes to ensuring quality in textile testing equipment, there are several key parameters that need to be considered. Firstly, accuracy is crucial. The equipment must be able to provide precise and reliable measurements to ensure accurate testing results. Secondly, repeatability is important. The equipment should be able to produce consistent results when the same test is repeated multiple times. Thirdly, durability is essential. Textile testing equipment is often subjected to heavy use, so it must be able to withstand wear and tear without compromising its performance. Lastly, ease of use is a key parameter. The equipment should be user-friendly and intuitive, allowing operators to easily navigate and operate it without any complications. By considering these parameters, manufacturers can ensure that their textile testing equipment meets the highest standards of quality.
Types of Testing Equipment Used in Textile Quality Assurance
In textile quality assurance, various types of testing equipment are used to ensure the quality and performance of textile products. One commonly used equipment is the tensile testing machine, which measures the strength and elasticity of fabrics and yarns. Another important equipment is the color fastness tester, which assesses the colorfastness of textiles to various factors such as washing, light, and rubbing. The pilling tester is used to determine the resistance of fabrics to pilling, while the abrasion tester measures the durability of textiles against abrasion. Additionally, the moisture management tester evaluates the moisture-wicking properties of fabrics. These testing equipment play a crucial role in maintaining the quality and reliability of textile products.
Challenges and Solutions in Maintaining Quality in Textile Testing Equipment
Maintaining quality in textile testing equipment poses several challenges for manufacturers and users alike. One of the main challenges is ensuring the accuracy and reliability of the equipment. Textile testing equipment needs to provide precise measurements and consistent results to ensure the quality of the textiles being tested. Regular calibration and maintenance are essential to address this challenge. Another challenge is the rapid advancement of technology, which requires manufacturers to constantly update their equipment to keep up with industry standards. Additionally, the complexity of textile testing processes and the variety of textiles being tested can also pose challenges. However, with proper training and expertise, these challenges can be overcome, ensuring the quality of textile testing equipment and the accuracy of test results.
Role of Calibration and Standardization in Textile Testing Equipment Quality Assurance
Calibration and standardization play a crucial role in ensuring the quality assurance of textile testing equipment. Calibration involves comparing the measurements of a device to a known standard to determine its accuracy. This process helps to identify any deviations or errors in the equipment’s readings, allowing for adjustments to be made to ensure accurate and reliable results. Standardization, on the other hand, involves establishing a set of guidelines and procedures that all testing equipment must adhere to. This ensures consistency and uniformity in the testing process, allowing for reliable and comparable results to be obtained. Overall, calibration and standardization are essential in maintaining the quality and reliability of textile testing equipment.
Future Trends in Textile Testing Equipment Quality Assurance
The future of textile testing equipment quality assurance is expected to be driven by advancements in technology and automation. With the increasing demand for sustainable and eco-friendly textiles, there will be a greater emphasis on testing for environmental impact and compliance with regulations. This will require the development of new testing methods and equipment that can accurately measure factors such as carbon footprint, water usage, and chemical content. Additionally, there will be a growing need for testing equipment that can handle the increasing complexity of textile materials, such as smart textiles and nanofibers. Overall, the future of textile testing equipment quality assurance will be focused on ensuring the production of high-quality, sustainable textiles that meet the needs of both consumers and the environment.
Conclusion
In conclusion, textile testing equipment plays a crucial role in ensuring the quality and safety of textiles. By conducting various tests and inspections, manufacturers can identify any defects or flaws in their products and make necessary improvements. This not only helps in meeting the regulatory standards but also enhances customer satisfaction and trust in the textile industry.
What is textile testing equipment?
Textile testing equipment refers to the instruments and machines used to evaluate the quality and performance of textiles. These equipment are designed to measure various properties such as strength, durability, colorfastness, and dimensional stability.
Why is quality assurance important in textiles?
Quality assurance is important in textiles to ensure that the products meet the required standards and specifications. It helps to identify any defects or flaws in the textiles before they are released into the market, thereby ensuring customer satisfaction and safety.
What are the common tests conducted using textile testing equipment?
Common tests conducted using textile testing equipment include tensile strength testing, colorfastness testing, abrasion resistance testing, pilling resistance testing, dimensional stability testing, and flammability testing.
How does textile testing equipment help in improving product quality?
Textile testing equipment helps in improving product quality by providing accurate and reliable measurements of various textile properties. This information can be used to identify areas of improvement, optimize production processes, and ensure that the final products meet the desired quality standards.
Who uses textile testing equipment?
Textile testing equipment is used by textile manufacturers, quality control departments, research laboratories, and regulatory bodies. It is also used by retailers and importers to verify the quality of the textiles they source from suppliers.
Where can textile testing equipment be purchased?
Textile testing equipment can be purchased from specialized manufacturers and suppliers of testing equipment. These companies often have a wide range of equipment options to choose from, catering to different testing requirements and budgets.