Industry 4.0, also known as the fourth industrial revolution, has brought about significant changes in various sectors. One area that has been greatly affected is the field of mixing and blending. This article will explore the impact of Industry 4.0 on these processes, including advancements in automation, data analytics, and predictive maintenance.
1. Introduction to Industry 4.0 and Its Relevance in Mixing and Blending
In today’s fast-paced and ever-evolving world, the concept of Industry 4.0 has become increasingly relevant, particularly in the field of mixing and blending. Industry 4.0 refers to the integration of advanced technologies such as artificial intelligence, robotics, and the Internet of Things (IoT) into industrial processes. This transformative phenomenon has a profound impact on the mixing and blending industry, revolutionizing the way products are manufactured and improving overall efficiency and productivity. As a professional in this field, I am excited to delve into the various applications and benefits that Industry 4.0 offers to the mixing and blending industry. From automated processes to predictive maintenance and enhanced data analysis, the possibilities are endless for revolutionizing the way we mix and blend different substances.
2. Automation and Robotics: Revolutionizing Mixing and Blending Processes
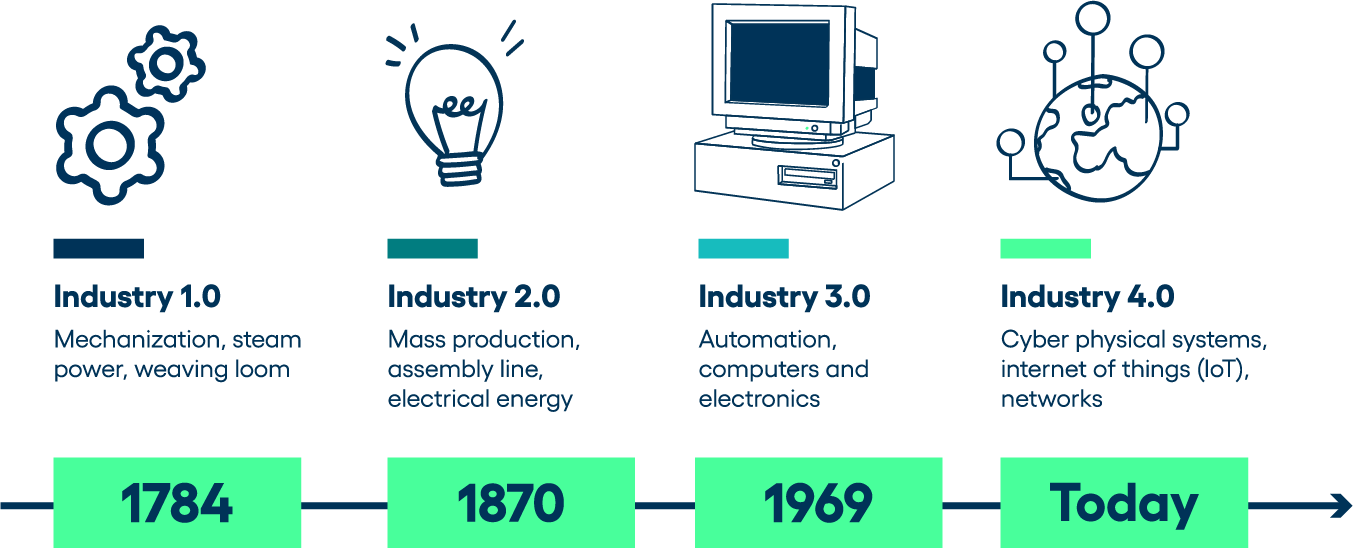
In my opinion, the use of automation and robotics in mixing and blending processes is truly revolutionizing the industry. As technology continues to evolve, it has become clear that these innovations not only increase efficiency but also improve the overall quality of the final product. Gone are the days of manual labor and human error; instead, we now have machines that can precisely measure and blend ingredients with utmost accuracy. These automated systems not only save time but also ensure consistency in every batch. Moreover, robots can handle tasks that were once considered dangerous for humans, further enhancing workplace safety. With automation and robotics, mixing and blending processes have reached new heights of productivity and reliability.
3. Big Data and Analytics: Enhancing Efficiency and Quality in Mixing and Blending
As a professional in the field of mixing and blending, I am constantly looking for ways to enhance efficiency and quality in my work. One of the game-changers in recent years has been the use of big data and analytics. By harnessing the power of data, we are able to gain insights into the variables that affect the mixing and blending process. This allows us to make more informed decisions and optimize our operations. From monitoring and controlling key parameters to predicting and preventing potential issues, big data and analytics have revolutionized the way we approach mixing and blending. Not only do they enable us to save time and resources, but they also ensure the consistent delivery of high-quality products to our customers.
4. Internet of Things (IoT): Connecting Mixing and Blending Machines for Seamless Operations
I am excited to talk about the fourth heading, which focuses on the Internet of Things (IoT) and how it is revolutionizing the way mixing and blending machines operate. With IoT, these machines can now be connected and communicate with each other, creating a seamless operation. This connectivity allows for real-time data collection, analysis, and adjustments, ensuring that the mixing and blending processes are efficient and consistent. It also enables predictive maintenance, as the machines can alert operators when servicing is needed, reducing downtime and increasing productivity. The IoT has truly transformed the manufacturing industry by enabling smarter, more connected machines for a smoother operational experience.
5. Cybersecurity Challenges in Industry 4.0 and Its Implications on Mixing and Blending
In today’s interconnected world, cybersecurity has become a growing concern for industries across the globe. With the advent of Industry 4.0, the integration of advanced technologies such as robotics, artificial intelligence, and the Internet of Things has brought numerous benefits to the manufacturing sector. However, it has also introduced new challenges, particularly in the area of mixing and blending processes. As a woman working in this field, I have witnessed firsthand the implications of these challenges on the security of our operations. The reliance on automated systems and interconnected devices leaves us vulnerable to cyber threats that can compromise the integrity and safety of our products. It is crucial for manufacturers to invest in robust cybersecurity measures and educate their workforce about the importance of maintaining a secure environment in an increasingly digital and interconnected world.
6. Future Prospects and Opportunities for Mixing and Blending in the Era of Industry 4.0
In the era of Industry 4.0, the prospects and opportunities for mixing and blending are abundant. With the advancements in technology and automation, there is immense potential to revolutionize the mixing and blending processes. The integration of smart machines and intelligent systems allows for precise control and optimization of the entire process, leading to enhanced efficiency, reduced waste, and improved product quality. Additionally, the use of data analytics and artificial intelligence enables real-time monitoring and predictive maintenance, ensuring uninterrupted operations. Moreover, the introduction of collaborative robots and automated guided vehicles presents opportunities for flexible and adaptive production, catering to the changing demands of the market. Overall, the era of Industry 4.0 brings with it a promising future for the field of mixing and blending, opening doors to innovation and growth.
Conclusion
In conclusion, Industry 4.0 has had a significant impact on the mixing and blending industry, leading to increased efficiency, accuracy, and productivity. Automation and digitization have revolutionized the way mixing and blending processes are performed, allowing for greater precision and control. As this technological revolution continues, it is crucial for businesses in the industry to embrace these advancements in order to remain competitive and meet the evolving needs of customers.
What is Industry 4.0?
Industry 4.0 refers to the fourth industrial revolution, characterized by the integration of advanced automation, data exchange, and manufacturing technologies. It encompasses the use of technologies such as the Internet of Things (IoT), artificial intelligence (AI), cloud computing, and advanced robotics to create smart and interconnected manufacturing systems.
What is mixing and blending in the context of industry?
Mixing and blending refers to the process of combining different materials or ingredients to create a homogenous mixture. This process is commonly used in various industries such as food and beverage, pharmaceuticals, chemicals, and cosmetics to ensure consistent quality and optimal product performance.
How does Industry 4.0 impact mixing and blending processes?
Industry 4.0 has a significant impact on mixing and blending processes by introducing advanced automation and control systems. These systems enable real-time monitoring and adjustment of process parameters, leading to improved accuracy, consistency, and efficiency in mixing and blending operations.
What are the benefits of incorporating Industry 4.0 in mixing and blending?
Incorporating Industry 4.0 technologies in mixing and blending processes offers several benefits. These include enhanced process control, reduction in human error, increased productivity, improved product quality and consistency, reduced waste and resource consumption, and the ability to adapt to changing market demands quickly.
What challenges may arise when implementing Industry 4.0 in mixing and blending?
Implementing Industry 4.0 in mixing and blending processes may pose certain challenges. These can include high implementation costs, the need for skilled operators and technicians, potential cybersecurity risks, compatibility issues with existing infrastructure, and the need for proper data handling and analysis capabilities.
Are there any examples of Industry 4.0 technologies in mixing and blending?
Yes, there are several examples of Industry 4.0 technologies being applied in mixing and blending processes. These include the use of sensor-equipped machines to measure and adjust mixing parameters in real-time, predictive maintenance systems to minimize downtime, cloud-based platforms for remote monitoring and control, and AI-powered algorithms for optimizing mixing recipes and process parameters.